摩擦顆粒料在現(xiàn)代摩擦材料中廣泛運用,它對改善摩擦材料的摩擦磨損性能,如制動效能,衰退,噪音等都有非常重要的作用,本文作者通過對有摩擦顆粒的摩擦材料的測試,結(jié)果表明,摩擦顆粒料是改善摩擦材料的性能的一種可行的方法之一。
隨著汽車工業(yè)的迅速發(fā)展,對車輛的安全性和舒適性的要求越來越高。摩擦材料對車輛的安全性和舒適性有非常大的影響,特別強調(diào)摩擦材料要具有穩(wěn)定的摩擦系數(shù),其中包括摩擦系數(shù)對壓力的穩(wěn)定性,盤式剎車片在制動時壓力可高達到50Mpa。摩擦系數(shù)對速度的穩(wěn)定性,其制動速度高達225公里/小時。摩擦系數(shù)對溫度的穩(wěn)定性,由于頻繁的連續(xù)制動,其剎車鼓表面恒定溫度高達700度。許多大的摩擦材料公司都用臺架試驗制動時剎車鼓變?yōu)榧t色的圖片作為其技術(shù)水平高的象征。以宣傳其剎車片高溫時的制動性能。由于這樣的工況,對摩擦材料的摩擦性能提出了非常高的要求。由于車輛的增加,車輛的噪音嚴重污染環(huán)境,高速制動時的摩擦穩(wěn)定性和震動對安全也有非常重要的影響。摩擦顆粒在現(xiàn)代摩擦材料中為改善摩擦材料的上述性能起到了非常重要的作用。十多年來,摩擦顆粒中的使用迅速發(fā)展??芍^異軍突起。幾乎歐美等各國的摩擦材料制造商都廣泛使用。特別是歐洲比較著名的大公司,在負荷較重的盤式剎車片中都有加入不同的摩擦顆粒。
一、基本工藝:
摩擦顆?;窘M分可以根據(jù)需要而不同,一般含有粘合劑如液體樹脂,橡膠或其他有機粘 圖1 摩擦顆粒的圖片 合劑,高炭材料,如石墨,焦碳等,摩擦調(diào)整劑,纖維等。經(jīng)過混合,造粒,干燥等工藝制成。見圖1。
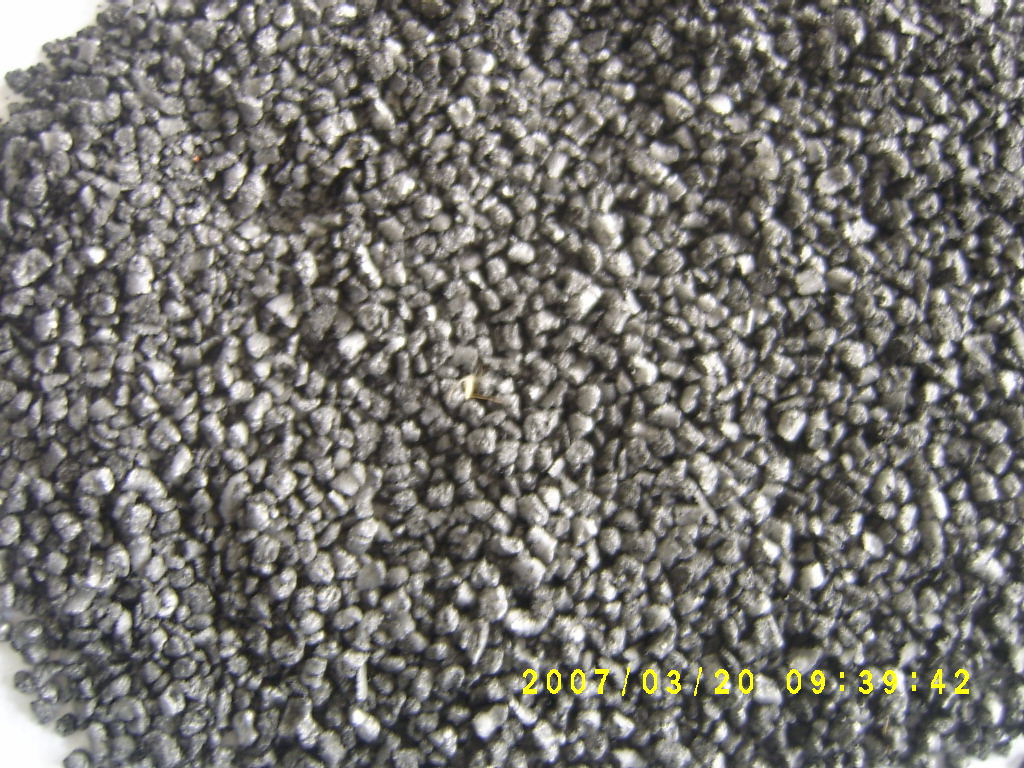
試驗用具有代表性的含有摩擦顆粒的盤式剎車片基本配比如下:
各種纖維?10-30%,
潤滑劑和填料?10–50%,
粘合劑?5-10%
摩擦顆粒?5-20%
其他摩擦性能調(diào)整劑和填料?適量
2:基本工藝:混料—壓制—-熱處理
二:試驗方法和結(jié)果:
1:按照國標GB5763-1998
汽車用制動器襯片的試驗方法,測試其摩擦系數(shù)和單位功的體積磨損率10-7cm3/Nm,同時還測試了每一個溫度條件下的重量磨損(克)和根據(jù)重量磨損的重量計算的體積折算磨損率10-7cm3/Nm。和由重量磨損折算的體積磨損率的比較評估。重量磨損折算體積磨損率由下式計算 △V2=((△WH265)/(Wμ125)
其中:△V2由每一個溫度下的重量磨損折算的體積磨損率10-7cm3/Nm
△?W 每一個溫度下的重量磨損?克
H?樣品的平均厚度?毫米
μ?每一個試驗溫度的平均摩擦系數(shù)
,試驗結(jié)果見圖2
2、按照QC/T 564/1999轎車制動器臺架試驗方法舉行臺架試驗和按照QC/T582-1999 J轎車制動器性能要求對試驗結(jié)果進行評估。
試驗結(jié)果見圖3.
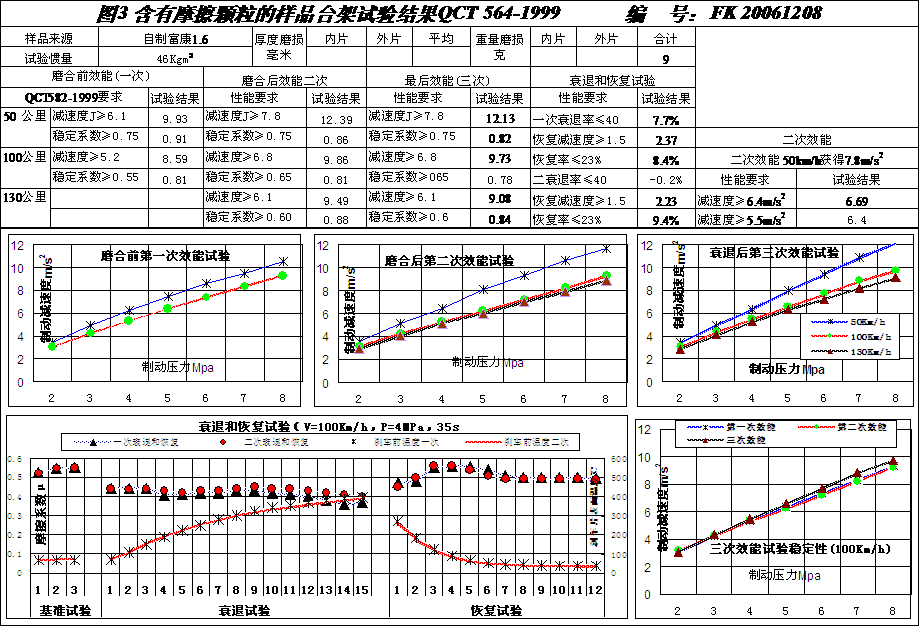
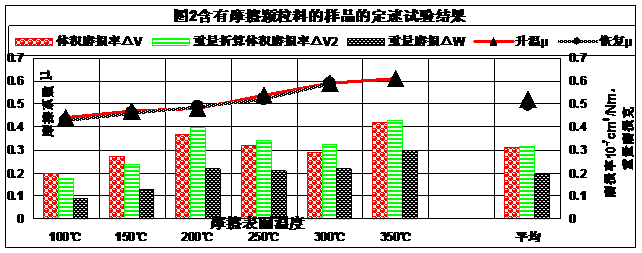
三、試驗結(jié)果討論:
從試驗結(jié)果看,使用摩擦顆粒的盤式剎車片,無論是定速試驗和臺架試驗,都有比較穩(wěn)定的摩擦系數(shù),臺架試驗中制動力矩穩(wěn)定系數(shù)也比較好,衰退和恢復(fù)試驗也比較好,特別是衰退試驗,最低的摩擦系數(shù)接近0.4.,其恢復(fù)性能都比較穩(wěn)定.由于摩擦顆粒的主要成分是炭,根據(jù)需要也要加入一些有機粘合劑,如彈性和韌性比較好的材料。試驗結(jié)果表明,雖然加入了這一類材料,但在衰退試驗中表現(xiàn)了良好的抗衰退性能?;謴?fù)性能也沒有影響。
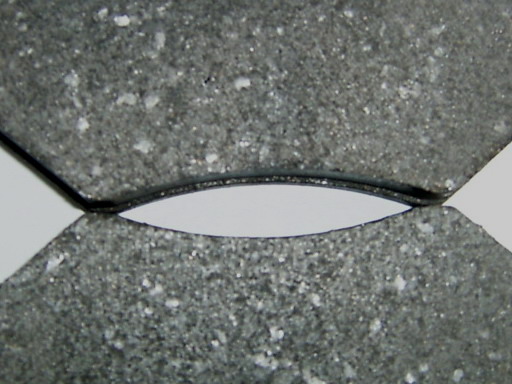
摩擦顆粒干燥時使用低溫烘干,這樣在樹脂含量比較的的配方中比較容易和其他料結(jié)合,由于加入了一些纖維和使用造粒,可以避免顆粒料表面過于光滑。提高與其他材料的粘結(jié)能力,提高耐磨性。由于目前的這種摩擦顆粒是比較大的顆粒炭,可以減少由于炭含量太高而導(dǎo)致的制動效能降低,保證制動性能的穩(wěn)定性。同時可以降低主體配方的粘結(jié)劑的用量。左面圖4是用摩擦顆粒和特種纖維的復(fù)合材料的陶瓷型盤式剎車片的圖片。
由于顆粒料的特殊工藝和一些特特殊的材料,如人造石墨,特種的潤滑劑,摩擦控制添加劑等。其氣孔率比一般的石墨顆粒高。高的氣孔率對改善摩擦性能,
降低指導(dǎo)噪音是比較重要的。摩擦過程是一個非常復(fù)雜的物理化學過程光靠一種材料是不能解決的,因此配方的調(diào)適十分重要,如樹脂含量,型號,纖維選擇,潤滑劑選擇,工藝,干法或濕法,冷壓,溫壓或熱壓。
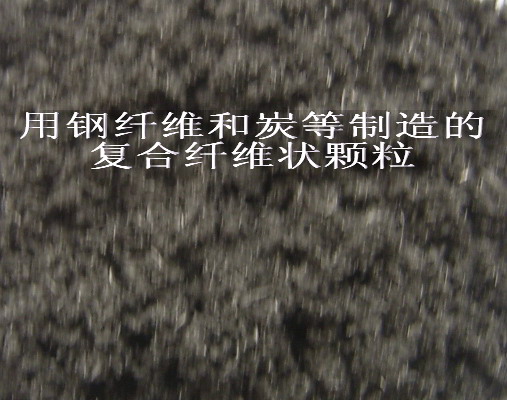
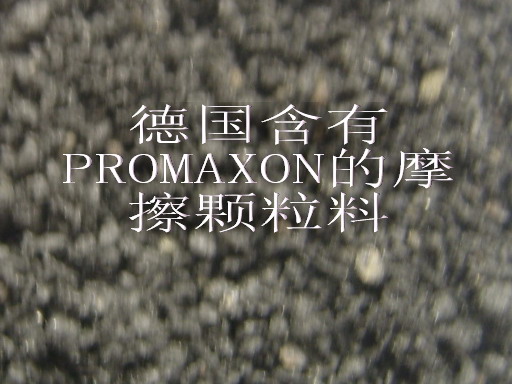
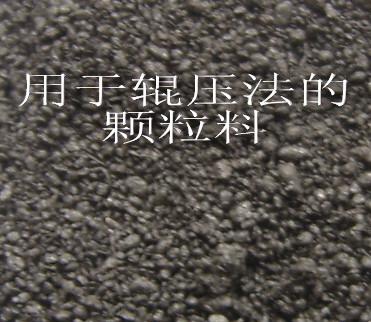
另外,可以根據(jù)客戶的要求,制成各種不同特性要求的摩擦顆粒,如不同的顏色,不同的摩擦特性,如高摩擦的,低摩擦的,軟質(zhì)的硬質(zhì)的纖維團的,橡膠基的樹脂基的和各種無機和有機黏合劑的,不同的粒度等等。下面是幾種摩擦顆粒的照片。
如德國的顆粒料,含有promaxon 等特別輕的填料,輥壓法的顆粒料可以直接輥壓成型或冷壓成型。也可以作為予混料加入到其他料中復(fù)合,以改變混合料的工藝性能,如流動性,,彈性硬度等,鋼纖維和炭等復(fù)合可以改變纖維方向,提高耐磨性,制動效能,噪音,克服半金屬摩擦材料的部分缺點,以及降低成本,由于顆粒料可以自成體系,可以彌補主體配方的不足,起到相輔相成的作用。提高摩擦顆粒的含量可降低磨損,我們用20%的摩擦顆粒混合料的盤式剎車片按照SAEJ661a試驗方法測試的摩擦性能如下:常溫摩擦系數(shù)0.33,熱摩擦系數(shù)0.32,摩擦級別EE級,重量磨損百分比1.09%,厚度磨損百分比0.96%??梢娔p是工藝降低的。
由于顆粒一般要用液體的黏合劑,因此混合的工藝和設(shè)備也需要進一步的試驗研究。如混料機的選擇,加料順序和混合工藝方法,如何制造更好造顆粒的設(shè)備,干燥方法等。
以前,國內(nèi)外有些工廠用密閉式煉膠機制造顆粒料,這種工藝設(shè)備投資費用比較高,如以前日本的α纖維,(一種含有橡膠和纖維的顆粒料),含有橡膠的粉碎料等,近幾年來,由于混料機技術(shù)和原材料工業(yè)的發(fā)展,液體黏合劑的品種已有比較大的發(fā)展,如各種液體樹脂,橡膠,以及無機和有機高分子材料。以及各種新的摩擦材料原料,使得比較容易的制成摩擦材料的顆粒料。這樣可以用比較低成本和裝備制造出合適的摩擦顆粒。
四、結(jié)論
- 摩擦顆粒料是改善摩擦材料的性能的一種可行的方法之一
- 對于顆粒的配方體系以及作用機理需要進一步的試驗研究。
- 混合工藝和設(shè)備需要進一步研究和完善。
發(fā)表于《摩擦密封材料2007第3期》